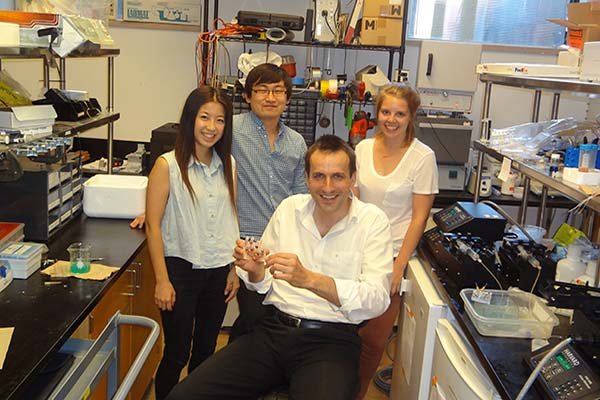
Second skin: U of T invention offers hope for burn victims
Published: January 22, 2013
Tissue engineering has taken a big leap forward with the University of Toronto invention of a process that can create functional replacement skin quickly and inexpensively.
The one-step device is believed to be the first in the world to create tissue rapidly on a large scale – important in repairing skin destroyed by burns or other major wounds. It’s hoped that, in future, instead of traditional skin grafts that remove patients’ own healthy skin for transplant, patients will receive machine-made skin grafts that are safer, faster and cheaper.
Graduate students Lian Leng, Boyang Zhang and Arianna McAllister contributed to the invention in the labs of Axel Guenther and Milica Radisic, professors at the Institute of Biomaterials and Biomedical Engineering. Their work is now attracting widespread attention.
Leng, a PhD student in microfluidics and the lead on the project, explains that the core of the printer is a small, unassuming-looking rubber device (below, right) with seven tiny wells. Each well holds a different biologically compatible polymer solution preloaded with molecules or cells, such as skin cells. The liquids are then extruded through the device, forming a soft, pliable, continuously flowing sheet of artificial skin full of living cells.
Unlike the “scaffolding” method of tissue creation, where a structure is created and then cells planted onto it afterward, this method seeds cells right into the sheet at the same time it’s being created. This dramatically increases the precision of the cell placement, which is important to allowing the cells to function normally, and to enabling the fabricated tissue to mimic natural tissue.
As the sheet of skin rolls out, it’s collected on a rotating drum, which produces multiple layers like plastic wrap on a roll, up to several centimetres thick. Until now, tissue could be created only in samples a fraction of that size. Thicker tissue is needed for sustaining blood vessels. Ironically, Leng, a mechanical engineer, had no experience with cell culture before helping to design the device.
“Someone had to show me how to culture and feed cells,” she says.
Last winter she spent months checking the cells daily to ensure they survived, attached and thrived.
Not only is the device faster and more precise than other tissue “printers,” it’s also much cheaper.
“Compared to other printers, which cost about $200,000, even by the most conservative estimates this one will produce tissue at a thousandth of the cost,” says Radisic.
The university has filed two patents on the invention, which is being commercialized by MaRS Innovations in collaboration with U of T's Innovations and Partnerships Office to sell to other research institutes and hospitals. While replacement skin is the focus now, future applications may include replacing cardiac tissue damaged by heart attacks. Preclinical trials will begin at U of T this year.
See more coverage of the story here.