Copper-coated face masks could help slow transmission of COVID-19: U of T researchers
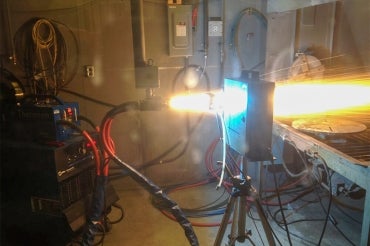
Published: September 4, 2020
A team of researchers from the University of Toronto’s Faculty of Applied Science & Engineering are developing a new way to coat tiny particles of copper onto the inside of fabrics, including those used in face masks – a technology that could provide an extra layer of safety against COVID-19.
The goal is to deposit very fine copper particles onto both woven and non-woven fabrics using twin-wire arc (TWA) spray technology. The fabric would then be used in one of the layers of a reusable fabric face mask. It’s anticipated the copper-embedded fabric will not affect filter or flow rate parameters and will be able to kill most viral and other pathogens within a few minutes.
By embedding the copper into the fabric, the researchers say masks could provide a continuous and proactive fight against the transmission of current and evolving harmful pathogens without altering the physical barrier properties of the masks themselves.
“If we can harness the anti-microbial properties of copper to improve the effectiveness of reusable face masks we can significantly reduce the spread of COVID-19 and do a better job at protecting both our frontline workers and our community at large,” says Javad Mostaghimi, a professor in the department of mechanical and industrial engineering.
The anti-microbial properties of copper have been observed since ancient times. Egyptian and Babylonian soldiers would place bronze shavings in their wounds to reduce infection and speed up healing. Today, Mostaghimi and his team – including Engineering’s Mohini Sain and Larry Pershin, James A. Scott of the Dalla Lana School of Public Health and Maurice Ringuette of the department of cell and systems biology in the Faculty of Arts & Science – are exploiting the very same anti-microbial properties to develop coatings that safeguard everything from office furniture to personal protective equipment.
Mostaghimi directs the Centre for Advanced Coating Technologies (CACT) and has studied the impact of copper coatings on infections in health-care settings for years, seeing first-hand how copper coatings applied to high-touch surfaces can help kill bacteria.
In one study, a copper coating was applied to the handles of half the chairs in a Toronto General Hospital waiting room. Over the course of five months, researchers recorded a 68 per cent reduction of viable bacteria cells per square centimetre on the treated chair handles.
Research from other groups shows COVID-19 surviving up to two to three days on stainless steel and even longer on other surfaces. However, it has been demonstrated that coronavirus particles are inactivated within four hours when exposed to a copper-coated surface at room temperature.
“Traditionally, implementing copper coatings would be very expensive,” Mostaghimi explains. “But our research has developed a method that makes applying copper coatings more economically viable.”
The CACT method is known as twin-wire arc spray. The “wire” part refers to the fact that the raw copper is supplied in the form of copper wire, which is more affordable than copper powders. The spray allows for large surfaces to be coated efficiently.
Another advantage is that the TWA method allows for spray parameters to be tightly controlled so that even heat-sensitive surfaces – wood, fabrics, even cardboard – can be coated.
Mostaghimi and his team were awarded an Alliance Grant from the Natural Sciences and Engineering Research Council of Canada (NSERC) to explore the possibility applying the TWA method to create copper-embedded fabrics for manufacturing reusable face masks.
For their project, titled “Copper Embedded Fabrics and Face masks for Rapid, Irreversible Destruction of COVID-19,” Mostaghimi and his team are collaborating with Green Nano Technologies Inc., which will produce a pilot run of the copper embedded face masks.
“Using our TWA spray technology, we will be able to produce copper-embedded masks at a marginally more expensive cost than N95 surgical face masks,” says Pershin, CACT’s centre manager.
“Additionally, as copper degrades both DNA and RNA genetic material, the masks will have the added benefit of irreversibly inactivating all microbial pathogens, regardless of their mutation rates even after masks were disposed.”
Various copper concentrations will be tested on the fabrics to help determine the optimal parameters for destroying the virus. The copper-embedded fabrics will be tested by Ringuette, whose team will use the fluid released from ruptured virus-infected bacteria, called bacteriophage lysates, to simulate SARS-CoV-2 on the masks.
The research has potential health and safety benefits that could extend well beyond the current pandemic. Affordable, reusable anti-viral PPE for health-care workers could mean a decrease in disease transmission in health-care facilities and a reduction associated infections.